Wednesday, December 29, 2010
Haven't Posted For a While
I am also currently building a website jeffguin.com. Right now I am just figuring out how I want the site set up so I am creating pages and links and adding photos of pottery that I have made in the past. The site tends to change every day but hope to finish it up soon.
Outside of my activities stated above, I plan on finishing the fiber lid for my brick wood burning kiln, clean and tune-up a treadle wheel that is sitting in the studio, fire up the fiber raku kiln, clean the studio, throw some pots---Well, lets just say I'd better get to doing and stop the "planning."
Tuesday, August 31, 2010
Wood Kiln

Plans are good but don't count on following them to "the letter." It ain't gonna happen. My original plans that I drew up don't look like this kiln at all, except that it is 8 feet long and the walls are about 24 inches tall.
Fire bricks are not the same size. They might look like it and might stack nicely on pallets but they definately aint the same size.
Assume from the beginning of the project that you're going to be a brick short. That goes for mortar too. If you're cutting brick, you're going to cut a bunch of them wrong. In fact, just think that you don't have enough of everything on the purchase list to complete the project.
The next step for this project is to purchase some insulating material for the arch and the sides of the kiln. I am thinking about about a home-made mixture of Diotomaceous Earth and Fire Clay, four parts to one.
After work today I am going to light up a fire in this puppy and see how it works. Basically I am just going to play around with the inlet flues and see how the chimney drafts.
Tuesday, August 10, 2010
Tapered Chimney

Monday, August 09, 2010
Wood Kiln Chimney Flues

I'm getting closer to finishing the mortaring. Here is the chimney and flues. One mistake I made was that I did not tie in the first layer of bricks that sit atop the flue brick into the walls of the kiln. I say "Just deal with it."
The measurements at this point are: inside is 23 inches wide and 18 inches tall. The chimney is 8 inches deep and 23 inches wide. This is the point where I am going to start tapering my chimney to get to a 9 by 9 inch hole.
The flues are 7 inches tall. The center flue is 2.5 inches wide and the others are 1-3/8 inches. I didn't follow any principles from any books regarding flue size and intake holes. I just built them based on photos I've seen of other kilns and figured better too big than too small.
Today, if the rain holds off, I hope to finish the tapered chimney and the front of the kiln.
Sunday, August 08, 2010
Wood Kiln Construction

Changes, changes, changes. I spent the last two years bugging people about kiln design and construction, looked at bunches of books, plans, etc.....and have come to the conclusion--If you want to build a kiln "JUST START BUILDING!"
I'm serious. Nothing goes according to "plan" and if you stick to that plan and are convinced to follow that plan and make it work---well, more power to you. Its just a big headache. In fact its just a pain in the ass. Have an idea and just start building and solve the problems as they come up.
In this case I've finally started mortaring the brick. Mix is one part sand, 2 part fire clay. I've never really mortared brick before so I took it slow mixing up very small batches in a 5 gallon bucket, although I only mixed about 1/2 gallon of mortar at a time when I first started. Stuff drys fast and I was by myself--a true tyro.
As I was saying. Just build it. The dimensions have changed everytime I put them on paper. Once the bricks were stacked and mortared my dimensions are: 32 inches wide and 81 inches long (outside dimension). Ware chamber is 18 inches tall in this photo but will be 20.5 inches, and 23 inches wide when complete, (approx 9.5 cubic feet). And its 35-1/2 inches long. The fire box is 24 inches long by 23 wide by 20-1/2 inches tall.
I'm still planning on one-inch thick kiln shelves for the roof, layered with soft brick and fiber on top of that.
Still working on the front part of the kiln. Right now I am going to tie-in all the brick and create a door with some air holes in the front.
I should mention that the base is 36 cinder blocks and on top of that a bunch of house brick, then the fire brick. The exterior of the kiln will have a 2 inch layer of insulating material of some sort. Oh! and I did incorporate 2 peek-holes on each side. One in front of the fire box area and one higher against the back wall. I plan on using soft brick to fill these holes.
I'll post some info on the chimney and flues in my next post. But this is where I'm at, at the moment, But, everything is subject to change.
Friday, July 30, 2010
Mouse hole/Grate system
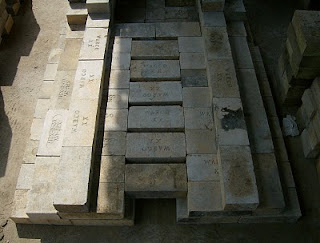
Tuesday, July 27, 2010
Wood Kiln Number One
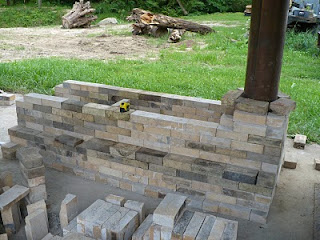
Thursday, July 08, 2010
Ramona Raku Kiln

This is my fourth garbage can raku kiln I have made since 2006. I have the complete steps with photos posted on this blog dated Jan. 2006. My first kiln lasted about 2 years. It seemed like I was firing it up every weekend all year long and it also sat outside in the yard. I called it Rusty Raku. One day I forgot to plug the hole and some critters got in and tore up all my fiber. So I built another.
The second kiln lasted about a year but was taken out by a major flood, the kind they say happens once in 100 years. Nothing to cry about. I built another. Less than one year later that once in a 100 year flood struck again, although not as bad, but it still took out my kiln. That was was my fault though because I had a hasty trip to make to the west coast and I forgot to bring my kiln into the studio. Anyway, I built another and am getting pretty good at it.
I call this one Ramona Raku. She is lined with two layers of one inch fiber which is held in place with a combination of sodium silicate and ceramic buttons that I made from heavily grogged raky clay. Looks great and I'm sure it will fire a lot better than my previous kilns, as they only had one layer of fire. Once I clean up my burner I'll fire her up and post some photos. Stay tuned.
Friday, June 11, 2010
Incense Bottle

Raku fired incense bottle, approximately 12 inches tall. What is an incense bottle? Well, you burn incense sticks in it. The end of the wooden stick is placed in a round clip, the incense is lit as normal and then dropped into the bottle. The round clip sits in the neck of the bottle. The incense burns upward and the smoke comes out of the top of the bottle neck. All the ashes fall into the bottom of the bottle. A very safe way to burn incense and I have recently found that there is a big demand for them.
The top of this bottle was glazed with clear crackle raku glaze and then lightly dipped in Green Apple raku glaze. The bottom was glazed with Green Apple as well.
Wednesday, June 09, 2010
Some New Pots

Tuesday, May 25, 2010
Pit Fire Colors
Wednesday, May 05, 2010
Pit Fire

The pit was only about one foot deep so we stacked some brick up to increase the depth to about two feet. I also brought my barrel and we did a barrel firing as well. All the pots around the pit are just pre-heating because we fired my raku kiln non-stop, load after load, till 1:30 in the morning. Once the top pots were removed from the top ledge of the pit and raku fired we placed a loosely fit tin cover over the pit and let it burn itself out. I'm guessing we had about 50 pots in the pit. Some were wrapped in tin foil saggers, some had terra sigallata finishes, and some were just plain bisqued pots. We also sprinkled copper carb and some other "magic dust" around the pot to create colors. The good news is everybody had at least one piece that they were extremely happy about but all the pots looked great to me and we had no breakage. All in all I think we fired the raku kiln about a dozen times and between the three kilns fired about 150 pots. We're in the process of taking photos of the finished pots and when that
is done I'll post a slide show of some of our favorites. All I can say is that it was a fantastic and successful event. Stay tuned for the slide show.
Thursday, April 08, 2010
Homemade Pottery Tools

Anyway, if I'm not getting muddy in the studio, at least I'm getting dusty.
Sunday, March 28, 2010
A Few Raku Pieces to Fire

Just a few raku pieces that need to be fired. The two figures were made last year. The little one was carved out of porcelain. The other one was just my regular stoneware clay body. Both were glazed with clear crackle raku glaze. The covered container was dipped in clear crackle raku glaze and the top portion and lid dipped in a "mystery" scrap glaze. The masks are porcelain and were made from plaster molds. They're fragile right now. I'm not sure how they'll handle the raku kiln. All three were dipped in clear crackle. The two tea bowls are glazed with clear crackle and the rims dipped in different "mystery" glazes. I also have some other tea bowls to fire. Two of those are glazed with TAK White raku glaze. It is supposed to be a thick fat white glaze but the first time I used it it came out as a smooth glassy opaque white, not very "fat" at all. This time around I applied it super thick. We'll see what happens.
For the past two weeks I've been glazing a lot of pieces that I fired in the electric kiln yesterday. I fired to cone 05 and it took me 6 hours start to finish. It probably would have taken less than 6 hours but I noticed that two of my elements are either burned out or not working properly. Anyway, I'll open it up today and see how everything came out. I haven't used any of these glazes before. They are Amaco matt and gloss glazes that were given to me because they were "old." Yeah, they must have sat on the shelf for a few years or more, probably more. They were all brand new, never opened, but the water had evaporated and I had to spoon out each glaze, reconstitue, and run it through the sieve a few times. It took a lot of work, but they were free.
I have a few olive oil bottles, some coffee mugs, some incense burners, a spitoon, a yarn bowl for my mother, and a bunch of other small stuff.
I'm out of clay so hopefully I'll sell this stuff real quick, buy some more, and get back to kicking the wheel.
Friday, February 26, 2010
Raku Firing Video
Tuesday, February 02, 2010
Barrel Kiln
