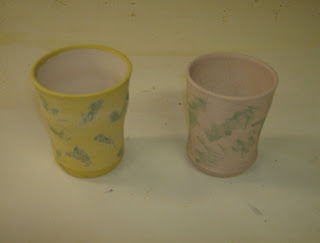
I don't know what the heck happened with this photo, but I'm not taking another one. Basically I just wanted to record what I'm doing so that if all turns out I'll remember what the heck I did.
These are two pieces of bisqueware that I have prepared for tin foil saggars. I didn't Throw the forms. These are just a couple of pieces that were going to be thrown out at the end of the semester. These cups had not been burnished.
The claybody is just a regular cone 10 stoneware, and probably bisqued to about cone 08.
The cup on the left was sprayed with a 50/50 mix of Ferric Chloride and water using a regular spray bottle. I think it was an old Windex bottle. The green markings are actually brush marks of Copper Carbonate and water, approximately 8 ounces water and 1 Tablespoon of Copper Carb.
The cup on the right was sprayed with a Cobalt Carbonate and water mixture, approximately 1 Tablespoon Cobalt Carb. and 8 ounces water. The same brush marks of the Copper Carb. and water were applied.
The next step is to wrap these pieces up in heavy duty tin foil. What I've read is that you crumple up the tin foil, uncrumple it and then wrap up the bique ware. In this case I am not adding any organic materials, although I might add some when it comes time to wrap them up. I'll keep notes. Stay tuned.
Many thanks to Aura Lee from Oregon. She has been reading my blog and also said she enjoyed reading it. Yeah! That's what I'm talking 'bout. Anyway she asked about my red raku glaze. I think the one she inquired about was a teabowl posted in Jan. 2007. I called it "Cabernet Red." No secrets here.
Cabernet Red Raku Glaze Recipe: as strange as it sounds it is approximately one handful of Burgundy Mason Stain to 3/4 of a plastic ice cream bucket of Soldners Clear Crackle Raku Glaze. I think I mixed a 2,000 gram batch of the clear, but it was about 3/4 full--80% Gerstley Borate, 20% Nepheline Syenite.
And once again, my raku firing has been delayed again. I usually get pretty fired-up when it comes to Raku-ing in the winter but lately it has been windy and cloudy. Oh! And cold too. I think the sun is supposed to come out today. Maybe today is the day.